What is Pipe Purging?
Purging a pipe prior to a weld is the act of displacing the atmosphere of a pipe or vessel and replacing it with another inert gas or in some cases a liquid. Purging is critical to the success of welding stainless steel, titanium or other corrosion metals.
Why Purge?
When welding stainless steel, titanium and other corrosion resistant materials, an inert environment for welding is high priority to retain the metals corrosion resistant properties. During the welding process the weld seam is subjected to heat and air which causes oxidation if the correct processes are not adhered to.
Oxidation is fundamentally the reaction of metal and oxygen and generally if the oxide formed is continuous and effective in separating the alloy from the atmosphere, the oxide is protective. However the hot area caused by welding process allows oxygen to interact with the metal to change its properties and then fails to act as a barrier. For the best weld appearance and life, the oxidation must be prevented.
Preventing Oxidation
During the welding of steels, oxidation occurs in the weld seam if oxygen reaches this area unhindered. This situation is even more acute with Stainless Steel, Titanium and other reactive metals and alloys. The resulting oxidized surfaces are no longer corrosion-resistant, and further treatment is necessary.
Removing oxidation by grinding can be done in certain circumstances but can also remove the metal's passive protection against corrosion. Other mechanical procedures, such as brushing, pickling acid can remove the oxidation as well which restores corrosion resistance. However, in some cases such as pipe welding, removing oxidation by these methods after welding is difficult or not economical to do. It can be impossible to successfully clean a weld in the middle of a long length of small diameter pipe.
Pickling paste will restore the corrosion resistance but it is time consuming and is a very hazardous process. Pickling pastes contain a combination of hydrofluoric acid and nitric acid which can cause serious burn injuries and the use and purchase of pickling paste is a controlled product in many countries. Weld Cleaning Machines are fast becoming the pickle paste substitute.
Instead of removing oxidation, another solution is to prevent it from occurring in the first place, as the old saying goes “Prevention is better than Cure” in essence, purging is a proactive rather than reactive approach which will provide a better outcome.
How Purging Works
With purging, an inert gas is used to protect the weld area until it has cooled to the point that oxidation no longer will occur. It removes the contaminating air from the piping and vessels to reduce chances of corrosion. Purging can also shield a hazardous environment when welding.
Argon is the most commonly used purging gas due to its low cost compared to the other gases that are available. Argon displaces the gases you do not always want near your weld pool such as nitrogen, carbon dioxide, and oxygen. Nitrogen is not suitable for stainless steel due to the gas will form nitrides and penetrate into the weld to increase the hardness of the steel. Carbon Dioxide will show similar results.
It is essential that when introducing the purging gas especially Argon that it is done gently to minimize turbulence of the exiting air. Argon is heavier than air so it should introduced at the bottom of the chamber and the air to exit towards the top of the chamber. Also when purging, maintaining a positive pressure is preferred, a positive pressure will displace other gases and maintain the integrity of the purge gas.
Purging Equipment
Taping up the ends with paper, tape or expanding plugs then purging the whole length of pipe is a simple, fast and common approach and in certain situations it can be enough but often this is an uneconomical process usually results in a lot of purging gas being used, unproductive labour time and an undesirable outcome. Proper equipment and accessories should include a reliable purging system, aluminum tape and a high quality oxygen monitor.
A popular purging system such as the TAG Double Inflatable Purging System is the most commonly used product in most situations due to their ease of use. Consisting of two inflatable bags (known as dams) that are connected by an inert gas tube about 400/500mm in length with one dam placed either side of the weld. The TAG Inflatable Pipe Dual Purge System has a luminous strip located in the middle of the gas tube for precise positioning. They greatly reduce the purge time and volume of gas required, provide a well-sealed environment and introduce no contaminants.
Most dedicated purging systems are designed that the purging gas is distributed at a slow enough speed within the purge chamber so that argon and oxygen mixing is reduced and excess turbulence is minimized; the key to high quality welds.
At the same time, the purging chamber should be sealed against further oxygen ingression. To speed up the purge time, the loss of argon should be reduced and fresh oxygen prevented from entering the weld area. To do this the pipe's joints should be sealed from the outside with a temperature resistant aluminum tape. Regular tape should not be used for sealing pipe gaps because these adhesives generally contain halogens, specifically chlorine. Chlorine, like hydrogen and oxygen, is absorbed by reactive metals at high temperatures, causing a poor weld.
All components used in the manufacture of purging units should therefore be halogen free, heat resistant and not containing dissimilar metals. An excess pressure vent also should be included to aid in the venting of oxygen and excess purging gas from the purged environment.
When welding corrosion-resistant materials and purging, it is important to be aware of the oxygen content that remains as this level must be blow certain parameters according to the base metal that you intend to weld. Oxygen levels are measured in PPM (Parts per million) Because of this, it is wise to monitor the complete procedure with an oxygen monitor. This sensor should be able to measure accurately to 1 part per million (PPM) oxygen.
Oxygen Monitors with capabilities of only 0.1 percent (1,000 PPM) or 0.01 percent (100 PPM) may not be accurate enough, as most precision welding is done well below 70 PPM. Higher accuracy makes it possible to find the source of each extra oxygen value and prevents weld failures and/or rework.
The length of purge time is another common issue. Besides using previous practical experience to determine purge time, welders can use many formulas that have been calculated to find the exact moment to weld. However, weld quality depends on many factors, including humidity, volume and material, just to name a few.
The correct length of time to typically purge is until the oxygen sensor indicates a value below 70 PPM for stainless steel or below 50 PPM for titanium. This can take up to 10 minutes depending on the size of the pipe when using a purging unit.
When welding with metals such as Titanium, a secondary inert shielding gas application is necessary to protect the cooling weld bead and heat-affected zone. A Trailing Shield can be attached to welding torches to follow behind as the weld is being made to improve weld purging on the front side of welds. In this way, the weld is kept under an inert gas shield for longer to allow the hot zone to be protected until cool enough to a safe temperature and prevent oxidisation in the surrounding air and hence giving an improved weld quality. It also allows the operator to weld quicker.
Chambers can be utilized when separate components require welding together, they can be placed inside a Weld Purging Chamber that is flushed out completely with inert gas. Sealed chambers are mostly used in very industry specific applications that are bespoke chambers but there are ready to use units also in the marketplace.
Weld Quality
Purging equipment and its use without any doubt has a major impact on preventing oxidation and improving final weld qualities. Many industries would not be viable without the ability and life of its infrastructure as what they are.
The effective welding of stainless steel, titanium, and their alloys for the nuclear, petrochemical, pharmaceutical, semi-conductor, aerospace and food industries requires the proper tools and a clean environment to create a perfect weld environment.
Operators should ensure that the purge cavity is always free from all excess items or residues that would risk the quality such as oil, paper, moisture, cloth etc. All such items will give off vapours when heated during the weld cycle and could risk contamination of the weld joint and rejection or failure of the weld when in use. Materials used should always be manufactured for the purpose of purging. All equipment especially gas related items must be kept free from moisture at all times.
Stainless Steel has the best indication of a good purge with post weld colours from silver to purple (silver being the best) to show a successful purge. See illustration below.
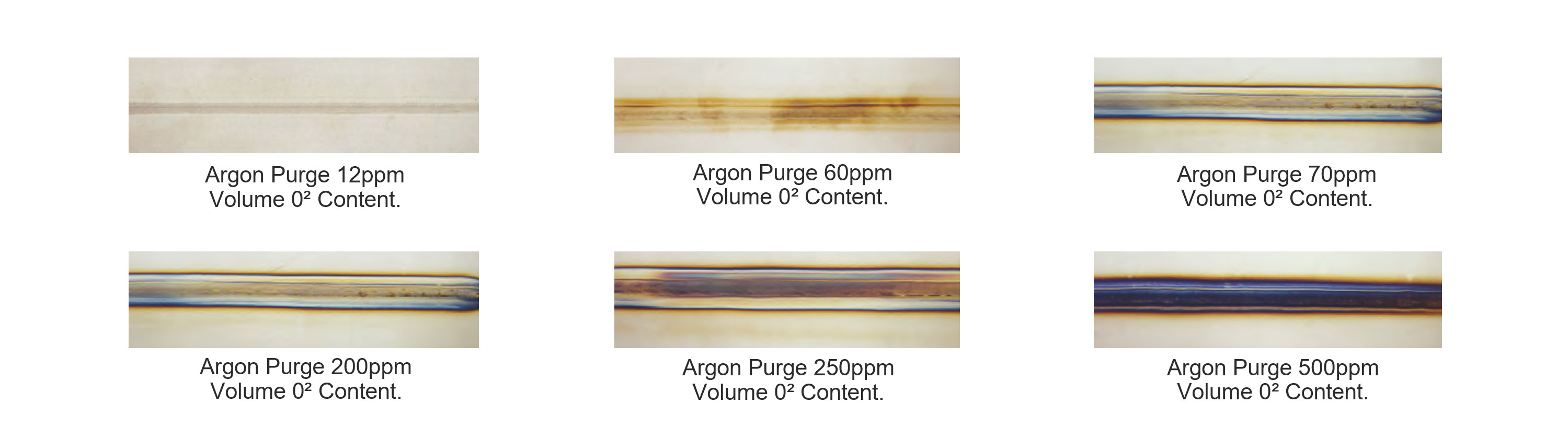
Conclusion
The expense of buying the correct purging equipment may seem a very high expense or outlay but the cost savings on labour, gas and time cannot be overlooked. The SC Profi Triple Seal System can pay for itself in 20 welds. It also be shot pipes including bends and elbows using compressed air for fast, precise positioning or the WS Plus Gas Cylinder Purging System is ideal for large pipes has been proved to pay for itself in less than 10 pipe welds.
Alphaweld has proved itself in many welding & purging related industries to be a valuable “go-to” solution provider and a stockist of many well known purging brands such as TAG Pipe and Walter Schnorrer.
Contact us today for answers to pipe purging on (08) 9456 8000.